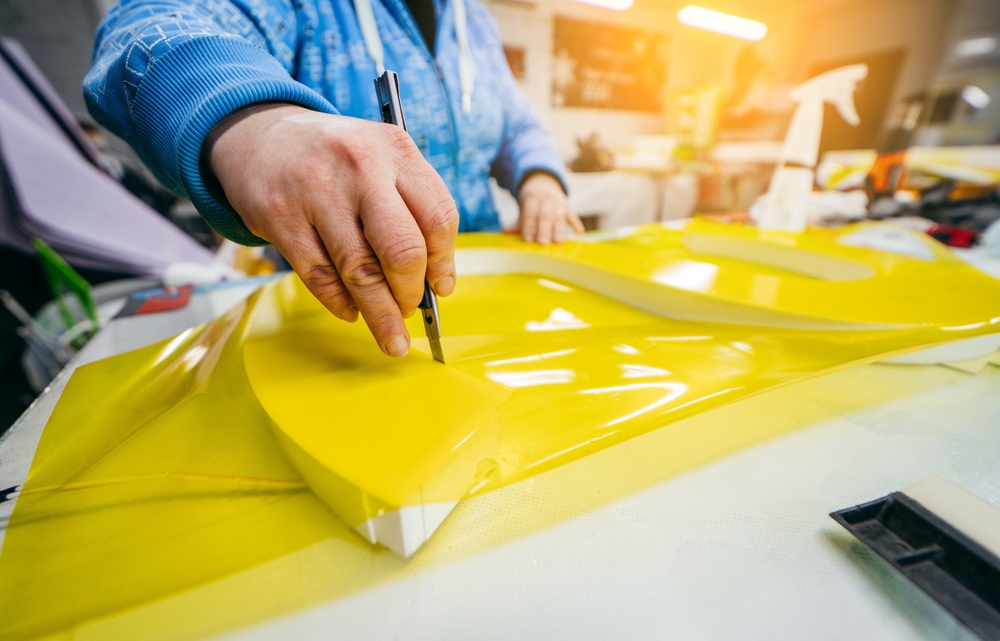
3D Printing vs. Traditional Machining
November 26, 2024 7:26 pm Leave your thoughtsIn the world of manufacturing, businesses and individuals often face a crucial decision: Should they opt for cutting-edge 3D printing technology or stick with tried-and-true traditional machining? Both methods have their advantages and challenges, but the choice ultimately depends on the project’s specific needs, time constraints, and budget. Whether you’re working with a machine shop or exploring modern fabrication tools, understanding the differences between these two processes will help you make an informed decision.
Understanding 3D Printing and Traditional Machining
Before diving into the comparison, it’s essential to understand what each method entails.
What is 3D Printing?
3D printing, also known as additive manufacturing, is a process where material is layered to create a three-dimensional object. A digital model serves as the foundation, and the printer adds successive layers until the design is complete. It’s a fast-evolving technology used for prototyping, small-scale production, and custom designs.
What is Traditional Machining?
Traditional machining refers to a subtractive manufacturing process, where material is removed from a solid block (metal, plastic, or other materials) using tools such as lathes, mills, and CNC machines. Local machine shops often use traditional machining to create precise and durable parts for industries ranging from automotive to aerospace.
Both methods aim to create functional components, but their processes and outputs vary significantly.
Key Differences Between 3D Printing and Traditional Machining
1. Material Versatility
- 3D Printing: While 3D printing has advanced significantly in terms of material options, it remains limited compared to traditional machining. Most 3D printers primarily work with plastics, resins, and, to a lesser extent, metals and ceramics.
- Traditional Machining: Machine shops have access to a wider range of materials, including various metals like aluminum, steel, brass, and titanium, as well as high-performance plastics and composites. This versatility makes traditional machining ideal for industrial-grade applications.
If your project demands specific materials or high-strength components, traditional machining from a local machine shop may be the better choice.
2. Precision and Tolerance
- 3D Printing: While 3D printing can achieve impressive detail, its precision is often limited compared to machining. Variations in layering and surface finish can result in tolerances that are less tight, making 3D printing less suitable for parts requiring extreme precision.
- Traditional Machining: Traditional machining excels in precision and tolerance. With tools like CNC machines, machine shops can produce parts with accuracy measured in microns. This is critical for industries where precision directly impacts performance and safety.
If your part requires tight tolerances and superior accuracy, traditional machining is likely the best fit.
3. Speed of Production
- 3D Printing: For small-batch production and prototypes, 3D printing is incredibly fast. Designs can be finalized in a digital format and printed within hours or days, eliminating the need for complex tooling.
- Traditional Machining: While traditional machining can also be quick, it often involves setup times, tooling, and machine calibration. However, once the process begins, traditional machining can produce large batches efficiently.
For rapid prototyping, 3D printing offers unmatched speed. However, for larger production runs, local machine shops using traditional machining can deliver consistent results in a timely manner.
4. Production Scale
- 3D Printing: Additive manufacturing shines in low-volume production and prototyping. It allows for cost-effective, custom parts without significant investment in tooling or molds.
- Traditional Machining: Traditional machining is far more efficient for medium to large production runs. Once the setup is complete, the per-unit cost decreases significantly as production volume increases.
If you need a few customized parts, 3D printing is ideal. But for bulk production, traditional machining from a machine shop is more economical.
5. Cost Considerations
- 3D Printing: The initial costs for 3D printing are lower because it does not require specialized tooling or molds. However, the per-unit cost can remain high, especially for larger projects or bulk production.
- Traditional Machining: While the initial setup cost may be higher due to tooling and machine programming, the cost per unit decreases significantly as production scales up. For high-volume projects, local machine shops offer better cost efficiency.
For businesses focused on long-term production goals, traditional machining often proves more cost-effective.
When to Choose 3D Printing Over Traditional Machining
3D printing has carved out its niche in the manufacturing world. Here are the situations where it excels:
Rapid Prototyping
When you need to create a prototype for testing or design validation, 3D printing delivers unmatched speed and flexibility. You can easily modify the digital model and reprint as needed without costly tooling adjustments.
Complex and Custom Designs
3D printing allows for intricate geometries that are challenging or impossible to achieve with traditional machining. From lattice structures to organic curves, 3D printing gives designers unprecedented creative freedom.
Low-Volume Production
For one-off parts or limited production runs, 3D printing eliminates the need for molds, reducing both time and costs. Custom and small-batch orders benefit greatly from this technology.
When to Choose Traditional Machining Over 3D Printing
Despite the rise of 3D printing, traditional machining remains the gold standard for many industries. Here’s why you might choose traditional machining:
High Precision and Tight Tolerances
When the application requires absolute precision, traditional machining ensures parts meet exact specifications. Industries such as aerospace, automotive, and medical rely heavily on the accuracy provided by local machine shops.
Strong and Durable Materials
If your project demands robust components made from metals like steel, titanium, or aluminum, traditional machining is the way to go. Machined parts are durable and perform well under extreme conditions.
Large-Scale Production
For high-volume production, traditional machining offers significant cost savings. Once the setup is complete, machine shops can produce thousands of identical parts efficiently.
Finding the Right Machine Shop
If you decide that traditional machining is the right choice, finding a reliable local machine shop is crucial. Local shops offer several benefits:
- Faster Turnaround Times: Working with a nearby shop reduces shipping delays and enables quick communication.
- Personalized Service: Local machine shops often provide tailored solutions and hands-on expertise to meet your project’s needs.
- Cost Savings: Partnering with a local shop can reduce transportation costs and streamline logistics.
Whether you’re a small business or a large enterprise, local machine shops ensure you receive high-quality parts with the precision and reliability you need.
Choosing the Best Method for Your Project
3D printing and traditional machining each have their strengths, and the right choice depends on your project’s unique requirements. If you need rapid prototypes, intricate designs, or low-volume custom parts, 3D printing is the ideal solution. On the other hand, for high-precision components, durable materials, and large-scale production, traditional machining from a trusted machine shop remains the superior option.
By understanding the strengths of each method and working closely with local machine shops, you can achieve high-quality results that meet both your budget and timeline. Whether you’re embracing additive manufacturing or relying on traditional techniques, the key is choosing the approach that aligns with your project goals.
Need Steel Fabricators in Hermiston, OR?
NW Metal Fabricators, Inc. is a family-owned business that has been servicing customers in Hermiston, Oregon since 1986. We have more than 100 years of experience in the food-processing industry and specialize in the custom production of storage bins, conveyors, catwalks, handrails, gates, storage tanks, water heater tanks, sanitary piping, steam piping, and trailer truck hitches. NW Metal Fabricators, Inc. is an accredited member of the local Chamber of Commerce. We are a dedicated business where quality always comes first. Our customers know that they can count on us to make sure that their products are hand-crafted to meet their specifications. Contact us today to learn more about what we can do for you!
Categorised in: Machining
This post was written by admin