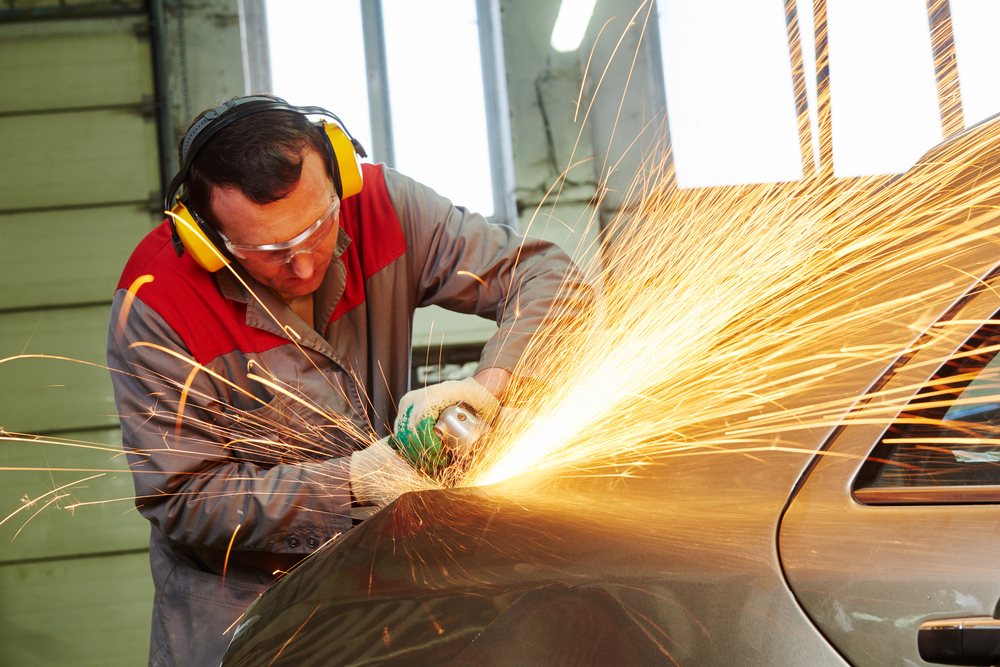
The Role of Welding in the Automotive Industry: From Parts to Performance
April 7, 2025 6:51 pm Leave your thoughtsThe automotive industry is one of the most complex and innovative sectors in the world, with each vehicle requiring precision engineering and state-of-the-art manufacturing processes. One such essential process is welding, which plays a crucial role in the assembly, repair, and performance of vehicles. From the body structure to internal components, welding ensures the integrity, safety, and durability of automotive products. In this blog, we will explore the significant role of welding in the automotive industry, shedding light on its impact on both manufacturing and repair processes.
The Evolution of Welding in Automotive Manufacturing
Welding has been an integral part of the automotive industry since the early days of car production. In the past, automotive manufacturers relied on manual welding techniques to join parts together. This method, though effective, was time-consuming and labor-intensive, requiring skilled technicians to ensure precision. However, over the years, technological advancements have revolutionized the automotive welding process. Automated robotic welding systems now dominate the industry, offering increased efficiency, consistency, and accuracy.
The introduction of advanced welding techniques such as laser welding, MIG (Metal Inert Gas) welding, and TIG (Tungsten Inert Gas) welding has further enhanced the precision and speed at which automotive parts are assembled. Laser welding, in particular, is favored for its ability to produce high-quality welds with minimal distortion, making it ideal for high-strength materials like aluminum and steel. As vehicles have become lighter and more fuel-efficient, the need for advanced welding techniques to work with modern materials has grown.
Automotive Welding Process: Key Applications in Manufacturing
The automotive welding process is employed in several key areas of vehicle production. The primary application of welding in manufacturing is in the assembly of the car body. Various components of the vehicle, such as the chassis, doors, fenders, and roof, are welded together to form the basic structure of the vehicle. This structural integrity is essential for the vehicle’s safety and overall performance. Automotive manufacturers use a combination of spot welding, seam welding, and robotic welding to achieve strong, durable bonds between components.
In addition to the exterior structure, welding is used in the production of critical internal parts, such as engine components, exhaust systems, and fuel tanks. These components require strong, reliable welds to withstand high temperatures, pressure, and vibration during the vehicle’s operation. In particular, exhaust systems often require precise welding to prevent leaks and ensure proper functioning.
Welding also plays a vital role in the production of lightweight vehicles. As the automotive industry shifts toward producing more fuel-efficient cars, the use of lightweight materials like aluminum and carbon fiber has increased. Welding techniques have had to adapt to these materials, which require different heat treatment and joining processes compared to traditional steel. For instance, aluminum welding requires precise control of heat to avoid distortion, while carbon fiber welding requires specialized equipment due to the material’s unique properties.
Welding for Automotive Repair: Enhancing Safety and Durability
While welding is essential in the manufacturing process, it is equally important in the automotive repair industry. As vehicles age, they inevitably undergo wear and tear, resulting in the need for repairs. Many automotive repair shops rely on welding to restore the structural integrity of damaged parts, whether from accidents, rust, or general use. Welding for automotive repair involves the same principles as welding during manufacturing, but the focus is on restoring or strengthening existing parts.
When a vehicle is involved in an accident, body panels, frames, and other structural components may suffer significant damage. In these cases, automotive welders are tasked with repairing or replacing these components to restore the vehicle to its original state. This process requires precise skill and knowledge of various welding techniques to ensure the vehicle’s safety. A poorly welded joint could compromise the car’s structural integrity, leading to safety risks for the driver and passengers.
Rust is another common issue in older vehicles, particularly in regions where road salt is used in the winter months. Over time, the metal parts of the vehicle can corrode, weakening the structure and potentially causing dangerous failures. Automotive welding is a crucial repair method for addressing rust damage, as it allows technicians to replace or reinforce corroded sections of the vehicle, ensuring that the car remains safe and functional.
In some cases, welding is also used to modify or upgrade a vehicle’s performance. For example, performance vehicles often require custom exhaust systems or modified frames to accommodate additional components such as turbochargers or suspension modifications. Welding allows for the precise fabrication of these parts, enabling automotive enthusiasts to personalize and enhance the performance of their vehicles.
The Impact of Welding on Vehicle Safety and Performance
Welding is directly linked to vehicle safety and performance. A well-executed weld ensures that a vehicle’s structure remains strong and intact during collisions, which is critical for passenger protection. Car manufacturers use advanced welding techniques to create crumple zones, which are designed to absorb the force of impact during an accident, preventing damage to the vehicle’s occupants. These crumple zones rely on carefully welded joints that are designed to bend and absorb energy in a controlled manner.
The quality of the welding also plays a significant role in the overall performance of the vehicle. Components such as the engine, exhaust system, and suspension rely on strong and durable welds to perform at their best. A failure in any of these parts due to poor welding could lead to a decrease in performance or, in some cases, a complete breakdown of the vehicle. For example, if the exhaust system is not properly welded, it can lead to exhaust leaks, which not only reduce the vehicle’s efficiency but can also result in harmful emissions that affect the environment.
In high-performance vehicles, where precision and reliability are paramount, the quality of welding becomes even more critical. Many performance vehicles, particularly sports cars and racing cars, use custom-welded components to enhance strength and reduce weight. These vehicles rely on advanced welding techniques to ensure that every part of the vehicle is optimized for speed, handling, and durability. For instance, welded aluminum frames are common in racing cars, as they provide a lightweight yet strong structure that can withstand the rigors of high-speed driving.
Future Trends in Automotive Welding: Innovation and Sustainability
As the automotive industry continues to evolve, so too does the role of welding. With the increasing demand for electric vehicles (EVs), manufacturers are exploring new welding techniques that can accommodate the unique materials used in EV production. For example, electric vehicles often use specialized batteries that require secure and reliable welding for safety. Battery enclosures must be carefully welded to ensure they are airtight and resistant to corrosion, as any leak or failure could lead to hazardous situations.
In addition to EVs, there is growing interest in the development of autonomous vehicles. As these vehicles require more complex electronic and sensor systems, welding technology must adapt to accommodate the integration of these new technologies. Precision welding is expected to play a crucial role in the production of the sophisticated parts that will be needed for autonomous vehicles, from sensors to battery systems.
Sustainability is also becoming an increasingly important consideration in the automotive industry. As consumers and manufacturers alike become more focused on reducing their carbon footprints, welding technology must evolve to meet these demands. This includes innovations in energy-efficient welding methods and the use of sustainable materials in vehicle production. Manufacturers are also exploring ways to recycle welded materials, reducing waste and minimizing the environmental impact of the production process.
Conclusion
Welding is an indispensable part of the automotive industry, playing a vital role in both manufacturing and repair. It ensures the strength, safety, and performance of vehicles, from their initial assembly to their eventual repair and upgrade. As the industry continues to innovate, welding technology will continue to evolve, supporting the development of new materials, vehicle designs, and sustainable practices. The future of automotive welding looks promising, with advancements that will drive the next generation of vehicles toward greater efficiency, safety, and performance.
Need Steel Fabricators in Hermiston, OR?
NW Metal Fabricators, Inc. is a family-owned business that has been servicing customers in Hermiston, Oregon since 1986. We have more than 100 years of experience in the food-processing industry and specialize in the custom production of storage bins, conveyors, catwalks, handrails, gates, storage tanks, water heater tanks, sanitary piping, steam piping, and trailer truck hitches. NW Metal Fabricators, Inc. is an accredited member of the local Chamber of Commerce. We are a dedicated business where quality always comes first. Our customers know that they can count on us to make sure that their products are hand-crafted to meet their specifications. Contact us today to learn more about what we can do for you!
Categorised in: Welding
This post was written by admin