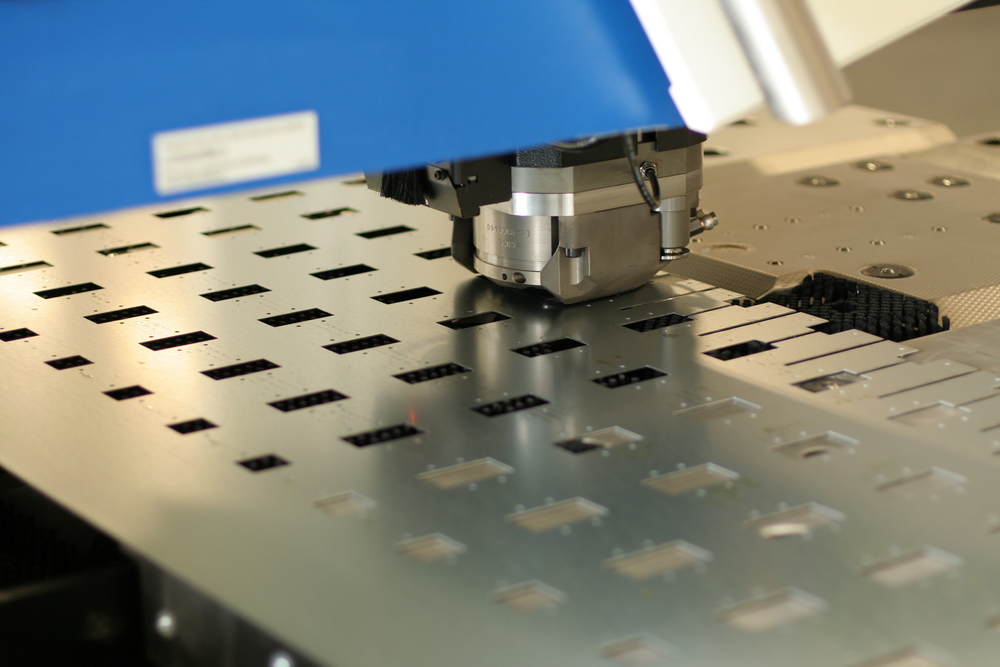
What is Shearing in Machining?
March 7, 2025 6:25 pm Leave your thoughtsShearing is a fundamental process in machining that plays a vital role in cutting, shaping, and forming materials. It is one of the most widely used methods in industries that deal with metalworking, automotive manufacturing, aerospace production, and various other sectors. By understanding the shearing process in machining, engineers and manufacturers can optimize their production processes to achieve high efficiency and precision. This blog delves into the mechanics of shearing, its applications, advantages, and types of shearing machines.
Understanding the Shearing Process in Machining
At its core, shearing is a cutting operation that involves the use of two blades to shear or separate material, typically metal, using a high force. In a typical shearing process, a material such as sheet metal or plastic is placed between two blades, which then apply pressure to the material. The force exerted causes the material to fracture along a defined line, creating a clean cut. This process is not a simple act of slicing but involves a significant amount of pressure, and the quality of the cut depends heavily on the sharpness of the blades, the material being cut, and the alignment of the shearing machine.
The shearing process is primarily used to cut thin materials like sheets and strips, but it can also be applied to thicker materials in more industrial settings. The most common shearing machines include guillotine shears, hydraulic shears, and mechanical shearing machines. These machines vary in the way they exert pressure on the material, but the general principle of shearing remains the same.
The Mechanics Behind Shearing Machines
Shearing machine operations are sophisticated and involve several critical components. At the heart of the process is the shear blade, which is responsible for making the cut. These blades are generally made of hardened steel to withstand the pressure and force applied during the operation. They come in different shapes and sizes, depending on the type of shearing machine and the material being cut. For example, some shearing machines may use a straight blade, while others may use a rotary blade to handle different types of material.
The shearing process operates through a shearing action that occurs when one blade moves towards a fixed blade, applying force to the material in between. The material, being held in place, experiences this force until it reaches a point where it can no longer withstand the pressure, causing it to fracture. This cutting action is generally a combination of shearing force and the geometry of the blade itself. By adjusting the gap between the two blades and the speed at which they move, manufacturers can control the quality and efficiency of the cut.
In some shearing machines, hydraulic systems are employed to generate the force necessary for cutting. These systems are highly effective, as they provide consistent and controlled force that can be fine-tuned depending on the thickness and hardness of the material. On the other hand, mechanical shearing machines use a system of gears and cams to generate force, making them more cost-effective but less precise than their hydraulic counterparts.
Applications of Shearing in Machining
Shearing is a versatile operation with applications across a wide range of industries. In the metalworking industry, it is primarily used to cut sheets, plates, and strips of metal to size. For instance, in the automotive industry, shearing is used to create parts such as chassis, body panels, and other components that require precise, straight cuts. In aerospace manufacturing, shearing is essential for cutting lightweight metals like aluminum to the required shapes and sizes. Additionally, the process is crucial for the fabrication of structural components used in buildings and bridges.
Shearing is also prevalent in the plastics industry, where it is used to cut plastic sheets, pipes, and profiles. The ability to create clean cuts without generating excessive heat is vital in ensuring that the structural integrity of the plastic is maintained. This also reduces the likelihood of deformities and stress fractures that may arise from other cutting methods, such as grinding or sawing.
Another key application of shearing is in recycling operations. Materials such as scrap metal, paper, and plastic are often cut into smaller pieces to facilitate easier handling, transportation, and processing. In such cases, large-scale shearing machines are employed to break down these materials into manageable sizes for further processing and reuse. The shearing process helps reduce waste and ensures that raw materials are efficiently utilized in various industrial applications.
Advantages of Shearing in Machining
The shearing process offers several significant advantages that make it a popular choice in various manufacturing and production settings. One of the primary benefits of shearing is its ability to deliver precise and accurate cuts, especially when it comes to thin materials. Since shearing involves the application of a focused force over a specific area, it produces clean edges and a high level of dimensional accuracy. This is essential for industries where tight tolerances are required, such as aerospace and automotive manufacturing.
Another advantage of shearing is its speed and efficiency. Unlike other cutting processes like sawing or grinding, shearing can produce cuts quickly, allowing for high throughput in production environments. Shearing machines can handle large volumes of material with minimal downtime, making it an ideal choice for mass production and high-volume operations. Additionally, the fact that shearing doesn’t generate heat means that there is less risk of material distortion or warping. This makes it particularly well-suited for cutting materials that are sensitive to temperature changes, such as plastics and metals with low melting points.
Shearing also offers cost advantages in terms of both the machinery and the energy required to perform the cuts. Mechanical shearing machines, in particular, are relatively inexpensive to purchase and maintain compared to more complex cutting technologies like laser cutting or waterjet cutting. Additionally, since shearing typically requires less energy than other methods, it is a cost-effective option for manufacturers looking to streamline their production processes without compromising on quality.
Challenges and Limitations of Shearing
Despite its many advantages, shearing is not without its limitations. One of the primary challenges of the shearing process is the potential for material distortion, especially when dealing with thicker materials or materials with inconsistent hardness. While the shearing process can produce clean cuts, it may sometimes result in burrs or edge deformation, particularly if the shearing machine is not calibrated correctly or if the material is of poor quality. To overcome this, manufacturers often use secondary processes, such as deburring or grinding, to smooth out the edges and ensure the desired finish.
Another limitation of shearing is that it is best suited for cutting materials of a certain thickness range. While it is ideal for thin sheets or strips, it may struggle with cutting thicker or harder materials. In these cases, alternative cutting methods like plasma cutting, laser cutting, or water jet cutting may be more appropriate, as they can handle a wider range of material thicknesses and hardness.
Furthermore, the design of the shearing machine and the type of blades used can significantly impact the quality of the cut. Machines with poorly maintained blades or improper blade alignment may lead to inconsistent cuts, increased wear, and frequent maintenance requirements. Ensuring that the shearing machine is well-maintained and the blades are sharpened regularly is essential for optimizing the process and ensuring high-quality results.
Conclusion
Shearing in machining is a critical process that allows for the precise and efficient cutting of materials, especially in industries like metalworking, automotive, aerospace, and plastics. By understanding the mechanics, advantages, and limitations of shearing, manufacturers can make informed decisions about the best cutting method for their operations. As technology continues to evolve, shearing machines and their capabilities will undoubtedly improve, offering even more advantages in terms of speed, accuracy, and efficiency.
Need Steel Fabricators in Hermiston, OR?
NW Metal Fabricators, Inc. is a family-owned business that has been servicing customers in Hermiston, Oregon since 1986. We have more than 100 years of experience in the food-processing industry and specialize in the custom production of storage bins, conveyors, catwalks, handrails, gates, storage tanks, water heater tanks, sanitary piping, steam piping, and trailer truck hitches. NW Metal Fabricators, Inc. is an accredited member of the local Chamber of Commerce. We are a dedicated business where quality always comes first. Our customers know that they can count on us to make sure that their products are hand-crafted to meet their specifications. Contact us today to learn more about what we can do for you!
Categorised in: Shearing
This post was written by admin