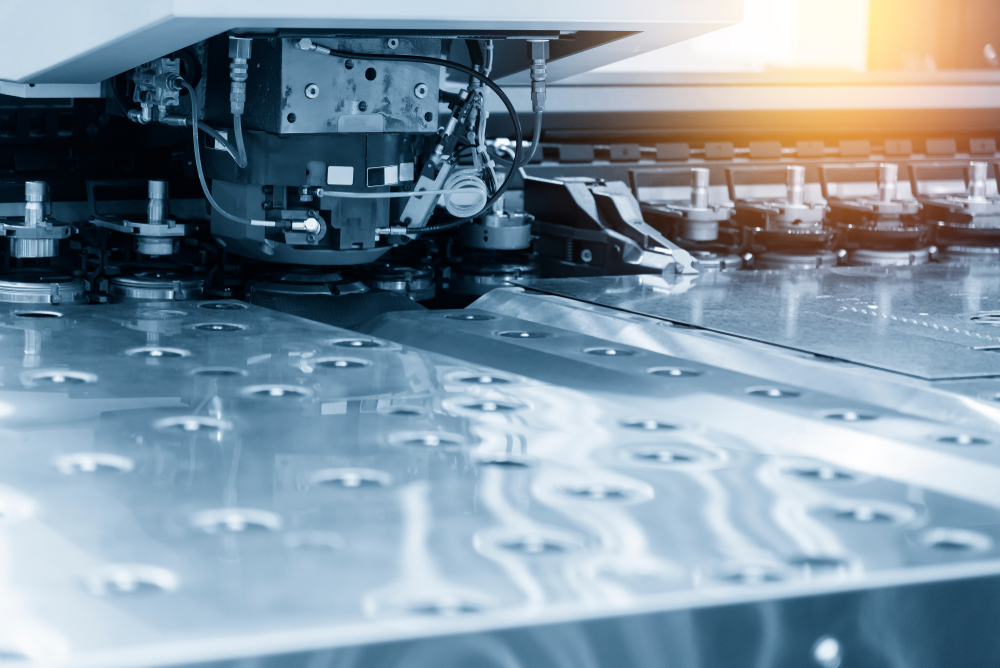
What Are the Advantages of Shearing in Machining?
March 7, 2025 6:25 pm Leave your thoughtsShearing is a popular machining process used in various manufacturing industries. It involves cutting or trimming a material by applying a high shear force to separate it into two distinct parts. This process can be done on a variety of materials, including metals, plastics, and composites, and is essential in applications ranging from automotive and aerospace to construction and electronics. Understanding the advantages of shearing in machining helps manufacturers make informed decisions about how to optimize their production processes. This blog explores the numerous benefits that shearing brings to the manufacturing industry.
Enhanced Precision and Accuracy
One of the key advantages of shearing in machining is its ability to produce highly precise and accurate cuts. The process involves sharp, clean blades that apply a controlled force to the material, ensuring that the cut edges are smooth and well-defined. Shearing can be performed with tight tolerances, which is critical in industries where even minor deviations can lead to significant performance issues. Whether it’s cutting metal sheets to size or trimming plastic components, shearing ensures that the dimensions of the material are consistent and precise.
This level of precision is essential in many applications, especially those that require high-performance standards, such as aerospace components, medical devices, or electronic enclosures. As a result, manufacturers can rely on shearing to meet the stringent quality control requirements that are often imposed by regulatory bodies. Shearing also minimizes the need for secondary finishing operations, saving time and reducing the overall cost of production.
Increased Efficiency and Speed
Another significant advantage of shearing in machining is the speed at which it can be performed. Compared to other cutting methods like milling or turning, shearing is a much faster process. This is particularly valuable in high-volume manufacturing environments where large quantities of material need to be processed in a short period. The speed of shearing allows manufacturers to meet tight production deadlines and increase overall throughput.
Shearing machines are typically designed to operate at high speeds, cutting through materials quickly without compromising the quality of the cut. The process is also automated in many cases, further enhancing efficiency. With the right setup, a shearing machine can process several pieces of material simultaneously, reducing the time spent on each part and further improving production efficiency. This increased speed makes shearing an attractive option for manufacturers who need to scale up their production or handle large orders.
Cost-Effectiveness in Production
Shearing is often considered a cost-effective machining process, especially when compared to other methods that require more complex machinery or more labor-intensive operations. The equipment used for shearing is typically less expensive than other machining tools, and the process itself requires less energy and maintenance. Because shearing is a high-speed process, it helps reduce the overall time spent on each operation, which can lead to significant savings in labor costs.
Additionally, the material waste generated by shearing is generally minimal. When cutting metals or other materials, shearing ensures that the majority of the material is retained, with minimal scrap produced. This reduces the overall material costs for manufacturers and helps them keep their production costs down. The combination of low equipment costs, reduced material waste, and fast processing times makes shearing an economically viable option for many manufacturing applications.
Versatility Across a Range of Materials
Shearing is incredibly versatile and can be applied to a wide range of materials. While it is most commonly used for metals like steel, aluminum, and copper, shearing can also be used on plastics, rubber, and other composite materials. This versatility makes it a go-to process for many different industries, from automotive to construction to electronics.
In addition to its material versatility, shearing can be used to perform various types of cuts, including straight cuts, curves, and notches. This flexibility allows manufacturers to tailor the process to suit their specific needs, whether they are creating complex shapes for aerospace parts or simple rectangular cuts for construction materials. The ability to adapt shearing to different materials and cutting needs makes it an indispensable tool in the manufacturing industry.
Minimal Heat Generation and Tool Wear
One of the advantages of shearing in machining that is often overlooked is the minimal heat generation during the process. Unlike cutting methods such as milling or grinding, where friction can lead to excessive heat buildup and tool wear, shearing produces very little heat. This is due to the nature of the process, where the material is sheared apart using a mechanical force rather than being cut or ground away.
The lack of heat generation has several benefits. First, it reduces the need for cooling fluids, which are often necessary in other machining processes to prevent overheating. This makes shearing a cleaner and more environmentally friendly option. Secondly, the reduced heat means that there is less risk of altering the properties of the material being cut. For example, metals can undergo changes in their hardness and structure if subjected to excessive heat, but with shearing, these risks are minimized. This helps ensure that the material retains its original strength and integrity.
Additionally, the reduced heat reduces tool wear, extending the lifespan of the cutting blades and reducing the frequency of tool replacements. This translates to cost savings for manufacturers and reduces the downtime associated with tool maintenance. The combination of minimal heat generation and low tool wear makes shearing a highly efficient and sustainable machining process.
Conclusion
Shearing offers numerous advantages in machining, making it a popular choice in a variety of manufacturing applications. Its precision and accuracy ensure that materials are cut to the exact specifications needed, while its speed and efficiency help manufacturers meet production demands quickly and cost-effectively. The versatility of shearing allows it to be used on a wide range of materials and for various types of cuts, further expanding its usefulness in different industries. Additionally, the minimal heat generation and reduced tool wear associated with shearing enhance its sustainability and reduce maintenance costs.
By understanding the advantages of shearing in machining, manufacturers can make informed decisions about when and how to implement this process in their operations. Whether the goal is to improve production speed, reduce material waste, or maintain high precision, shearing provides a reliable and efficient solution. As industries continue to evolve, the advantages of shearing in machining will remain a crucial factor in the success of many manufacturing processes.
Need Steel Fabricators in Hermiston, OR?
NW Metal Fabricators, Inc. is a family-owned business that has been servicing customers in Hermiston, Oregon since 1986. We have more than 100 years of experience in the food-processing industry and specialize in the custom production of storage bins, conveyors, catwalks, handrails, gates, storage tanks, water heater tanks, sanitary piping, steam piping, and trailer truck hitches. NW Metal Fabricators, Inc. is an accredited member of the local Chamber of Commerce. We are a dedicated business where quality always comes first. Our customers know that they can count on us to make sure that their products are hand-crafted to meet their specifications. Contact us today to learn more about what we can do for you!
Categorised in: Shearing
This post was written by admin