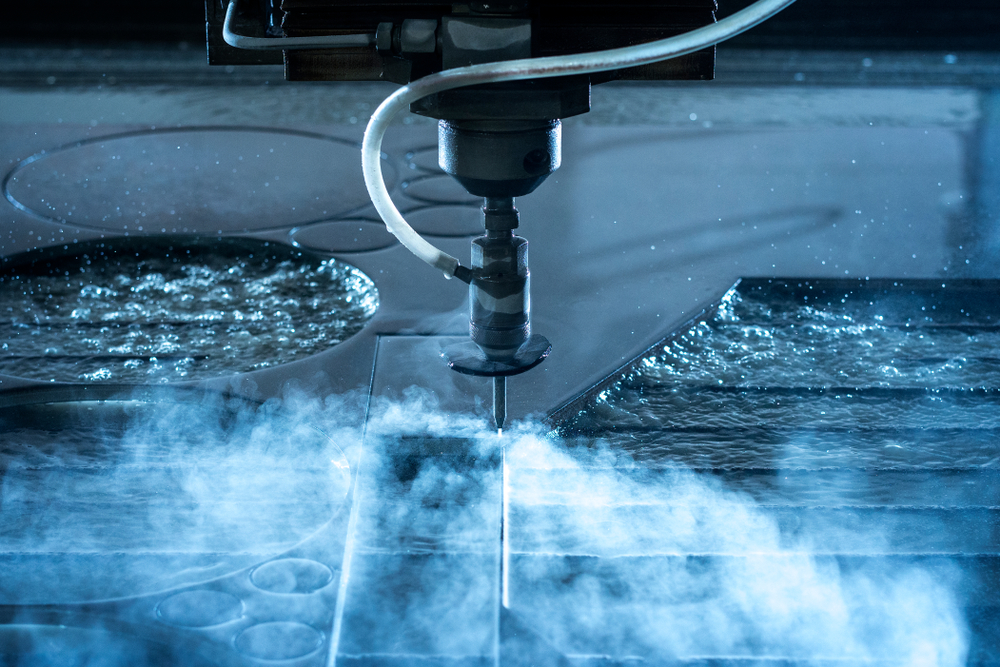
Top Materials That Can Be Cut Using Water Jet Technology
February 7, 2025 8:15 pm Leave your thoughtsWater jet cutting technology has revolutionized the manufacturing and fabrication industries by offering a versatile, precise, and efficient cutting method. Unlike traditional cutting techniques, which may involve heat or mechanical force, water jet cutting utilizes a high-pressure stream of water, sometimes mixed with an abrasive substance, to slice through a variety of materials with remarkable accuracy. This process minimizes thermal stress, reduces material wastage, and allows for intricate designs that might be challenging with other methods.
The versatility of water jet cutting is one of its greatest advantages, making it an ideal choice for cutting a wide range of materials. Whether soft or hard, thick or thin, water jet technology can handle a diverse set of materials with minimal environmental impact. Due to its adaptability and efficiency, this method is widely used in industries such as aerospace, automotive, construction, and even artistic applications. Understanding the types of materials suitable for water jet cutting is essential for maximizing the potential of this cutting-edge technology.
Metals and Alloys: Strength Meets Precision
Metals are among the most common water jet cutting materials due to the technology’s ability to create clean cuts without inducing heat-related damage. Traditional cutting methods, such as plasma or laser cutting, often introduce thermal stress that can alter the structural integrity of metals. In contrast, water jet cutting eliminates this issue, making it an excellent choice for working with metals and alloys.
Stainless steel is one of the most widely cut metals using water jet technology. It is commonly used in industries requiring corrosion-resistant and durable components, such as medical equipment, food processing machinery, and architectural structures. The precision of water jet cutting ensures smooth edges without the need for secondary finishing processes.
Aluminum, known for its lightweight and high-strength properties, is another metal that benefits from water jet cutting. The process enables manufacturers to cut intricate shapes without causing warping or deformation. This is particularly useful in the aerospace and automotive industries, where precision is critical.
Other alloys, such as titanium, brass, and copper, are also suitable for water jet cutting. Titanium, used extensively in aerospace and medical implants, requires precise cutting without compromising its strength. Copper and brass, often used in electrical components and decorative applications, benefit from water jet cutting’s clean cuts that preserve the material’s aesthetic appeal.
Ceramics and Glass: Delicate Yet Durable Materials
Water jet cutting is also highly effective for cutting fragile materials like ceramics and glass, which can be challenging to process using conventional cutting methods. The cold cutting nature of water jet technology prevents thermal cracking and ensures a smooth finish without compromising structural integrity.
Ceramic materials, widely used in the manufacturing of tiles, electronic components, and medical devices, require precise cutting to maintain their functionality. Traditional mechanical cutting tools often result in chipping or breakage, whereas water jet cutting delivers clean and accurate cuts with minimal waste.
Glass cutting is another area where water jet technology excels. From decorative glass panels to specialized industrial components, the precision of water jet cutting allows for intricate designs without the risk of cracking or splintering. This makes it an ideal method for creating custom glass pieces used in architecture, interior design, and automotive applications.
Tempered glass, stained glass, and laminated glass are all materials suitable for water jet cutting. The process allows manufacturers to create customized shapes and patterns with smooth edges, enhancing both functionality and aesthetics in various applications.
Composites and Plastics: Modern Solutions for Diverse Applications
Composites and plastics are increasingly used in various industries due to their lightweight, durability, and adaptability. Water jet cutting provides an effective way to shape these materials without generating harmful fumes or excessive heat, which could otherwise alter their composition.
Carbon fiber-reinforced plastics (CFRP) and fiberglass are widely used in aerospace, automotive, and sports equipment manufacturing. Traditional cutting methods often cause delamination or fraying of composite materials, leading to suboptimal performance. Water jet cutting, however, offers precise and clean cuts without compromising the material’s strength.
Plastics such as acrylic, polycarbonate, and polyethylene are also commonly processed using water jet technology. These materials are used in everything from signage and displays to industrial components and protective barriers. Water jet cutting ensures smooth and precise edges, reducing the need for additional finishing processes.
Thermoplastics, which soften when heated, are particularly well-suited for water jet cutting because the process does not introduce heat into the material. This makes it an excellent choice for applications where maintaining material properties is crucial, such as in medical devices and electronic enclosures.
Stone and Wood: Natural Materials with Customization Potential
Water jet cutting is not limited to industrial applications; it is also a valuable tool in artistic and architectural projects involving natural materials like stone and wood. The precision and flexibility of this technology allow for intricate designs, making it popular in both functional and decorative applications.
Stone materials, including marble, granite, and slate, are commonly used in construction and interior design. Water jet cutting provides a way to create custom shapes, engravings, and detailed inlays without the risk of cracking or breaking the stone. This method is widely employed in creating countertops, flooring, and intricate mosaics.
Wood cutting with water jet technology is gaining popularity in the furniture and decorative industries. While traditional woodworking tools can create precise cuts, water jet cutting allows for greater design complexity without the risk of burning or splintering. This is particularly beneficial for intricate carvings, customized furniture pieces, and artistic installations.
Even engineered woods, such as plywood and MDF (medium-density fiberboard), can be efficiently cut using water jet technology. The process ensures clean edges without fraying, making it an excellent choice for cabinetry, signage, and architectural applications.
The Future of Water Jet Cutting Materials
The expanding range of materials suitable for water jet cutting demonstrates the technology’s growing importance in modern manufacturing and design. As advancements continue, the potential for cutting even more materials with greater efficiency and precision will only increase. Industries ranging from aerospace and automotive to construction and artistic design continue to benefit from the flexibility, accuracy, and eco-friendly nature of water jet cutting.
With minimal material waste, reduced need for secondary processing, and the ability to handle both delicate and robust materials, water jet cutting remains an indispensable tool in precision fabrication. As research and innovation push the boundaries of this technology, we can expect even greater capabilities in the future, further enhancing its applications across various industries.
Need Steel Fabricators in Hermiston, OR?
NW Metal Fabricators, Inc. is a family-owned business that has been servicing customers in Hermiston, Oregon since 1986. We have more than 100 years of experience in the food-processing industry and specialize in the custom production of storage bins, conveyors, catwalks, handrails, gates, storage tanks, water heater tanks, sanitary piping, steam piping, and trailer truck hitches. NW Metal Fabricators, Inc. is an accredited member of the local Chamber of Commerce. We are a dedicated business where quality always comes first. Our customers know that they can count on us to make sure that their products are hand-crafted to meet their specifications. Contact us today to learn more about what we can do for you!
Categorised in: Water Jet Cutting Services
This post was written by admin