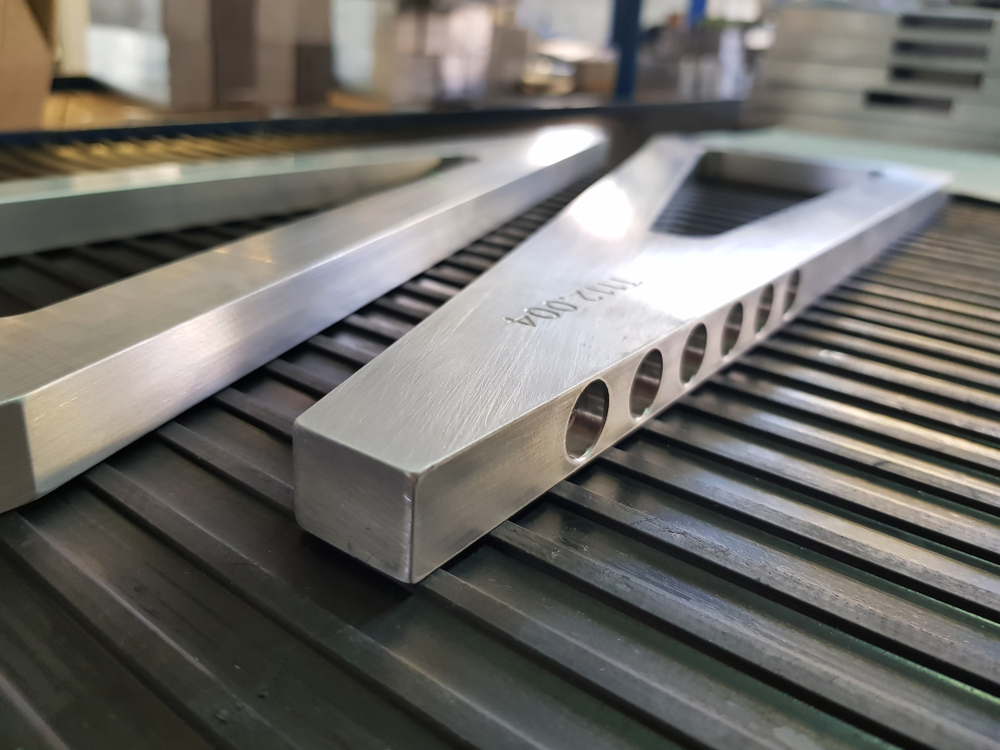
The Importance of Precision in Metal Fabrication: How We Ensure Quality
January 27, 2025 3:16 pm Leave your thoughtsMetal fabrication enables the creation of everything from industrial machinery to bespoke architectural elements. Whether crafting large-scale components or intricate custom designs, precision in metal fabrication is paramount. It ensures not only aesthetic appeal but also functionality, durability, and safety. In this blog, we explore the importance of precision in custom metal fabrication and the methods employed to guarantee high-quality outcomes.
Understanding Custom Metal Fabrication
Custom metal fabrication involves transforming raw metal into specific structures or products tailored to unique requirements. This process spans several stages, including cutting, shaping, assembling, and finishing. Each stage demands accuracy and attention to detail to ensure that the final product meets the desired specifications.
Key Elements of the Fabrication Process
- Design and Planning: Every custom metal fabrication project begins with detailed design and planning. Computer-Aided Design (CAD) software is often used to create precise blueprints and models that guide the manufacturing process.
- Material Selection: Choosing the right metal is critical. Factors such as strength, corrosion resistance, and weight are considered to match the material to the project’s requirements.
- Cutting and Shaping: Techniques like laser cutting, water jet cutting, and CNC machining are employed to shape metal components with high precision.
- Assembly and Welding: Components are joined together using advanced welding techniques, ensuring strong and durable bonds.
- Finishing: Processes such as polishing, coating, and painting enhance the product’s aesthetic and protective qualities.
Each step is interconnected, meaning that errors at any stage can compromise the quality and functionality of the finished product. This is why precision is indispensable.
Why Precision Matters in Metal Fabrication
The role of precision extends beyond aesthetics; it impacts the structural integrity, functionality, and longevity of the product. Here are the key reasons why precision is vital:
Ensuring Structural Durability
Durability in metal fabrication is closely linked to the accuracy of the process. Poorly cut or misaligned components can create weaknesses, compromising the structural integrity of the product. Precision ensures that every part fits perfectly and functions as intended, resulting in a robust and long-lasting structure.
Enhancing Functionality
In applications such as machinery, tools, or complex assemblies, even minor inaccuracies can lead to malfunctions. For example, improperly aligned components can cause friction, wear, or complete failure. By maintaining precision, custom metal fabrication delivers products that perform seamlessly under various conditions.
Aesthetic Appeal
Precision is equally important in projects where appearance matters, such as architectural installations or decorative elements. Clean lines, smooth finishes, and precise detailing contribute to the visual impact of the product, enhancing its overall value.
Cost-Effectiveness
While precision may require advanced tools and meticulous attention to detail, it reduces costly mistakes and rework. Accurate fabrication minimizes material waste and ensures that the product is built right the first time, saving both time and money.
Safety Compliance
Many fabricated metal products are used in critical applications, such as construction or transportation. Precision ensures compliance with safety standards, reducing the risk of accidents and ensuring the well-being of users.
Tools and Techniques That Ensure Precision
Achieving precision in custom metal fabrication relies on advanced tools, techniques, and skilled craftsmanship. Below are some of the key methods employed to ensure quality:
Advanced Machinery
Modern fabrication facilities are equipped with state-of-the-art machinery designed for accuracy and efficiency.
- Laser Cutting Machines: Provide precise cuts with minimal material waste.
- CNC Machines: Enable automated, highly accurate cutting, drilling, and milling operations.
- Robotic Welding Systems: Ensure consistent and high-quality welds, reducing human error.
Measurement and Quality Control Tools
To verify precision, measurement tools such as calipers, micrometers, and coordinate measuring machines (CMM) are used throughout the fabrication process. These tools allow for real-time adjustments, ensuring that components meet exact specifications.
Skilled Workforce
Even with advanced machinery, the expertise of skilled fabricators plays a critical role. These professionals understand the properties of different metals, interpret complex designs, and execute processes with meticulous attention to detail.
Quality Assurance Protocols
Comprehensive quality assurance processes are essential to uphold precision. Regular inspections, material testing, and adherence to industry standards ensure that the finished product meets all requirements.
Challenges in Achieving Precision
Despite advancements in technology, precision metal fabrication is not without its challenges. Addressing these issues requires proactive measures and continuous improvement.
Material Variability
Metals can vary in quality and composition, affecting their behavior during fabrication. Rigorous material selection and testing help mitigate this variability.
Complex Designs
As custom designs become more intricate, ensuring precision becomes more challenging. Advanced CAD software and simulation tools assist in planning and executing complex projects.
Equipment Calibration
Precision machinery requires regular maintenance and calibration to perform optimally. Neglecting this aspect can result in inaccuracies and delays.
Skilled Labor Shortage
The demand for skilled metal fabricators often exceeds supply, posing a challenge for many manufacturers. Investing in training programs and apprenticeship opportunities is crucial to building a capable workforce.
Innovations Driving Precision in Metal Fabrication
The field of metal fabrication is continuously evolving, with innovations aimed at enhancing precision and efficiency. Some of the latest advancements include:
Artificial Intelligence (AI) and Machine Learning
AI-powered systems analyze data from fabrication processes to identify patterns and optimize operations. Machine learning algorithms can predict potential issues, allowing for preemptive adjustments.
Additive Manufacturing
Also known as 3D printing, additive manufacturing enables the creation of complex metal structures with unparalleled accuracy. This technology is especially useful for prototyping and producing intricate components.
Internet of Things (IoT) Integration
IoT-enabled devices provide real-time monitoring of fabrication processes, ensuring precision at every stage. Sensors and connected systems enhance efficiency and reduce the likelihood of errors.
Advanced Welding Technologies
Techniques such as laser welding and friction stir welding offer superior precision and strength, expanding the possibilities for custom metal fabrication.
Case Studies: Precision in Action
Aerospace Components
In the aerospace industry, precision is non-negotiable. Fabricated metal parts must withstand extreme conditions and meet rigorous safety standards. Techniques like CNC machining and robotic welding ensure that these components are manufactured to exact specifications.
Architectural Installations
For projects like modern skyscrapers or intricate sculptures, precision fabrication ensures that each element fits seamlessly. Advanced cutting and finishing techniques contribute to the visual and structural integrity of these installations.
Medical Equipment
Metal fabrication is critical in producing medical devices and equipment, where precision directly impacts functionality and patient safety. Techniques like laser cutting and additive manufacturing are commonly used to create intricate components.
How We Prioritize Quality in Custom Metal Fabrication
At our facility, we are committed to delivering the highest standards of precision and quality in every project. Here’s how we achieve this:
Rigorous Planning and Design
Every project begins with detailed planning and design. Our team works closely with clients to understand their needs and create accurate blueprints using advanced CAD software.
Investment in Technology
We leverage cutting-edge machinery and tools to ensure precision at every stage of the fabrication process. From laser cutting to robotic welding, our equipment is regularly maintained and calibrated for optimal performance.
Skilled Craftsmanship
Our team of experienced fabricators brings a wealth of knowledge and expertise to every project. Their attention to detail ensures that each product meets or exceeds client expectations.
Comprehensive Quality Control
We implement stringent quality control measures, including material testing, dimensional checks, and final inspections. These protocols ensure that the finished product is both precise and durable.
Customer-Centric Approach
Understanding that every project is unique, we prioritize open communication and collaboration with our clients. This approach enables us to deliver custom metal fabrication solutions that align perfectly with their requirements.
Conclusion
Precision in metal fabrication is more than a technical requirement; it is the foundation of quality, durability, and functionality. From advanced tools and skilled craftsmanship to rigorous quality control, every aspect of the process contributes to achieving exceptional results. As custom metal fabrication continues to evolve, the emphasis on precision will remain central to meeting the ever-changing demands of modern industries. By prioritizing accuracy and investing in innovation, we ensure that our clients receive products that stand the test of time.
Need Steel Fabricators in Hermiston, OR?
NW Metal Fabricators, Inc. is a family-owned business that has been servicing customers in Hermiston, Oregon since 1986. We have more than 100 years of experience in the food-processing industry and specialize in the custom production of storage bins, conveyors, catwalks, handrails, gates, storage tanks, water heater tanks, sanitary piping, steam piping, and trailer truck hitches. NW Metal Fabricators, Inc. is an accredited member of the local Chamber of Commerce. We are a dedicated business where quality always comes first. Our customers know that they can count on us to make sure that their products are hand-crafted to meet their specifications. Contact us today to learn more about what we can do for you!
Categorised in: Metal Fabrication
This post was written by admin