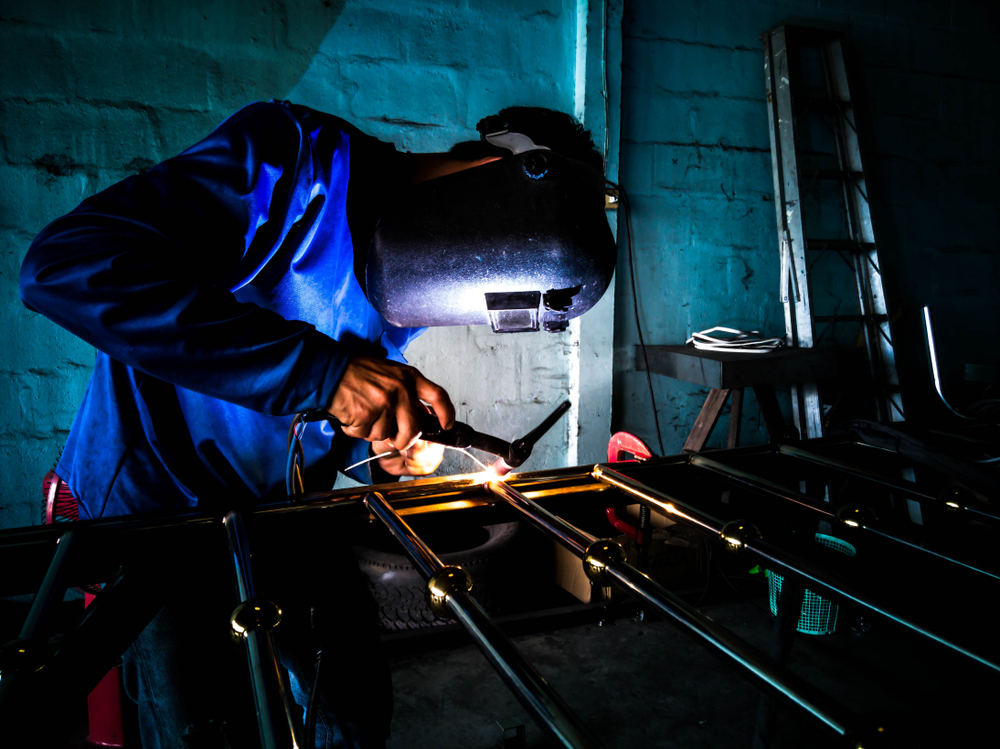
Aluminum Versus Stainless Steel in Metal Fabrication
October 8, 2024 4:20 pm Leave your thoughtsMetal fabrication is a cornerstone of many industries, ranging from construction and automotive to aerospace and consumer goods. Among the various metals used, aluminum and stainless steel are two of the most commonly chosen materials. Both metals offer unique advantages and drawbacks depending on the application, making the choice between aluminum and stainless steel in metal fabrication a critical decision. This blog delves into the differences between aluminum and stainless steel in metal fabrication, guiding you in making an informed choice for your next project.
The Basics of Metal Fabrication
Metal fabrication is a process that involves cutting, bending, and assembling metal to create structures, machinery, or components. Depending on the material, fabrication processes can vary in complexity, cost, and durability. Selecting the right metal is crucial as it impacts the longevity, strength, weight, and even aesthetic quality of the final product.
What is Stainless Steel?
Stainless steel is a popular metal alloy, primarily composed of iron, carbon, and chromium. The inclusion of at least 10.5% chromium makes stainless steel resistant to rust and corrosion, which is one of its key advantages. Its shiny appearance and high durability make it suitable for various applications, particularly in environments where exposure to moisture or corrosive substances is a concern.
What is Aluminum?
Aluminum is a lightweight metal known for its high corrosion resistance, especially in environments that are not suitable for steel or other metals. It is not as strong as stainless steel but can be made stronger through alloying with other metals like magnesium or copper. Aluminum is widely used in industries where weight is a significant factor, such as aerospace and automotive applications.
Key Differences Between Stainless Steel and Aluminum in Metal Fabrication
Both aluminum and stainless steel are integral to metal fabrication, but they differ in their properties, making them better suited to specific projects. Let’s break down the differences based on key attributes:
Strength and Durability
When it comes to strength, stainless steel metal fabrication typically produces more robust components than aluminum. Stainless steel’s high tensile strength makes it ideal for applications that require extreme durability, such as structural components in construction, heavy machinery, and industrial equipment. Its resistance to deformation under heavy loads ensures longevity, especially in high-stress environments.
Aluminum, while not as strong, has a much better strength-to-weight ratio, making it perfect for lightweight applications that still require durability. For example, aluminum is used in aerospace engineering and vehicle frames where reducing overall weight is crucial to improving performance and fuel efficiency.
Corrosion Resistance
Corrosion resistance is a top priority in industries where metals are exposed to moisture, chemicals, or extreme environmental conditions. Stainless steel excels in environments where rust or corrosion is a concern. Its chromium content forms a protective layer on the surface, preventing rust and other forms of corrosion. This property is why stainless steel is often used in kitchen appliances, medical devices, and outdoor structures.
Aluminum also boasts impressive corrosion resistance but in a different way. When exposed to air, aluminum forms a thin layer of oxide that protects the metal from further oxidation. However, aluminum’s resistance to corrosion diminishes in environments with high salinity or extreme pH levels, making it less suitable for marine applications unless it’s alloyed with other materials.
Weight
One of the most significant advantages of aluminum in metal fabrication is its lightweight nature. Aluminum weighs about one-third as much as stainless steel, making it a prime candidate for applications where weight reduction is critical. For example, in the aerospace and automotive industries, using aluminum reduces the overall weight of the structure, leading to improved fuel efficiency and reduced emissions.
Stainless steel, while much heavier, provides added strength and resistance to wear and tear. This makes it more suitable for applications that demand weight tolerance and robustness, such as heavy machinery and large-scale construction projects.
Conductivity
When it comes to electrical conductivity, aluminum outshines stainless steel by a significant margin. Aluminum is an excellent conductor of electricity, making it a go-to material for electrical applications like power lines and wiring. In contrast, stainless steel has poor conductivity, which limits its use in electrical applications. However, stainless steel’s thermal conductivity can be advantageous in certain industrial processes where heat resistance is required.
Machinability and Fabrication Process
The machinability of a metal refers to how easy it is to cut, shape, or weld. In general, aluminum is easier to machine than stainless steel. It is softer and requires less power to cut or form, reducing overall production costs and time. Aluminum can also be welded, though care must be taken to avoid defects like cracking due to its higher thermal conductivity.
On the other hand, stainless steel metal fabrication can be more challenging. Its high hardness and tensile strength mean that more powerful equipment is needed for cutting and shaping. Additionally, stainless steel’s lower thermal conductivity can lead to complications in welding, requiring more precise techniques to prevent warping or weakening.
Cost
The cost of materials is always a consideration in metal fabrication. Typically, stainless steel is more expensive than aluminum due to its higher strength, durability, and corrosion resistance. However, the higher upfront cost of stainless steel can often be offset by its longevity and lower maintenance needs in many applications. For example, stainless steel may require less frequent replacement or repair in corrosive environments, making it a more cost-effective solution over the long term.
Aluminum, being more affordable upfront, is often chosen for projects with tight budgets or when the lightweight nature of the material is a necessity. However, it’s important to consider that aluminum might not last as long as stainless steel in demanding environments, so maintenance and replacement costs should be factored into the overall budget.
Common Applications of Aluminum and Stainless Steel in Metal Fabrication
Both aluminum and stainless steel have their specific niches in various industries. Understanding where each metal is most commonly used can help in selecting the right material for your project.
Applications of Stainless Steel in Metal Fabrication
- Construction: Stainless steel’s strength and resistance to rust make it ideal for structural components in buildings, bridges, and industrial infrastructure.
- Medical Devices: Its non-reactive surface and ease of sterilization make stainless steel a favorite in medical equipment and surgical tools.
- Food and Beverage Industry: Stainless steel is extensively used in kitchen appliances, cookware, and food processing equipment due to its resistance to corrosion and ease of cleaning.
- Marine Applications: Stainless steel is preferred in environments where exposure to saltwater and moisture is constant, such as boat fittings and docks.
Applications of Aluminum in Metal Fabrication
- Aerospace Industry: Aluminum’s lightweight nature makes it indispensable in aircraft manufacturing, where reducing weight is key to enhancing performance.
- Automotive Industry: Aluminum is increasingly used in vehicle bodies and parts to reduce weight and improve fuel efficiency.
- Electronics: Due to its excellent electrical conductivity, aluminum is used in electrical components, wiring, and heat sinks.
- Packaging: Aluminum is widely used for packaging, particularly in the form of cans, foils, and other lightweight, durable containers.
Choosing the Right Material for Your Metal Fabrication Project
Selecting between stainless steel and aluminum in metal fabrication depends largely on the specific requirements of your project. If strength, durability, and corrosion resistance are paramount, stainless steel is likely the better option. It’s the material of choice for heavy-duty industrial applications, construction, and areas exposed to harsh environments.
However, if weight reduction, ease of fabrication, and conductivity are more critical factors, aluminum may be the superior option. It is ideal for aerospace, automotive, and electrical applications where performance and efficiency are key.
Conclusion
Both stainless steel and aluminum play essential roles in metal fabrication, each offering unique advantages that make them suitable for specific applications. Stainless steel is often chosen for its strength, durability, and corrosion resistance, while aluminum excels in lightweight, conductive, and cost-sensitive applications. Understanding the differences between the two metals can help you make an informed choice, ensuring your metal fabrication project meets both your performance and budgetary goals.
Need Steel Fabricators in Hermiston, OR?
NW Metal Fabricators, Inc. is a family-owned business that has been servicing customers in Hermiston, Oregon since 1986. We have more than 100 years of experience in the food-processing industry and specialize in the custom production of storage bins, conveyors, catwalks, handrails, gates, storage tanks, water heater tanks, sanitary piping, steam piping, and trailer truck hitches. NW Metal Fabricators, Inc. is an accredited member of the local Chamber of Commerce. We are a dedicated business where quality always comes first. Our customers know that they can count on us to make sure that their products are hand-crafted to meet their specifications. Contact us today to learn more about what we can do for you!
Categorised in: Metal Fabrication
This post was written by admin