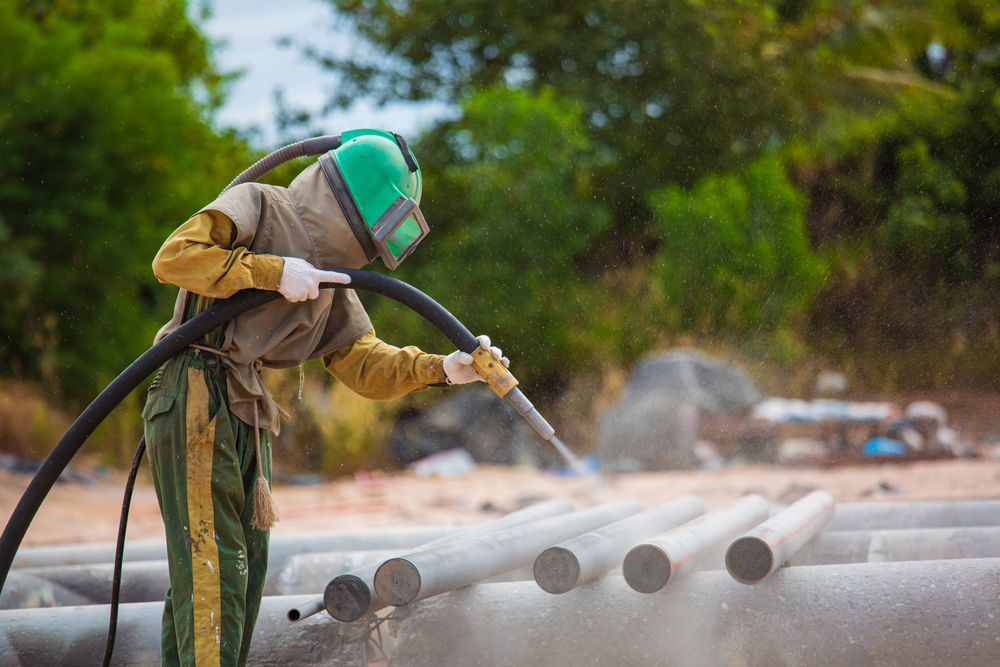
The Role of Sandblasting in Rust Removal and Corrosion Prevention
February 7, 2025 8:15 pm Leave your thoughtsRust is an inevitable problem for metals exposed to moisture and oxygen, causing structural damage and aesthetic issues over time. One of the most effective techniques for removing rust and preparing metal surfaces for protective coatings is sand blasting for rust removal. This process ensures thorough cleaning, eliminating contaminants and creating a surface suitable for adhesion. Understanding the role of sandblasting in rust removal and corrosion prevention helps industries and individuals maintain metal structures and extend their lifespan.
Understanding the Sandblasting Process
Sandblasting is an abrasive cleaning method that uses high-pressure air to propel fine particles, such as sand, aluminum oxide, or glass beads, against a surface. The impact of these particles removes rust, paint, and other contaminants, leaving a clean and smooth finish. The process is widely used in industrial applications, automotive restoration, and construction projects, providing a reliable solution for metal maintenance.
The effectiveness of sandblasting depends on several factors, including the type of abrasive used, the pressure applied, and the condition of the metal surface. Coarser abrasives remove thick rust layers quickly, while finer materials provide a polished finish without damaging the underlying metal. By carefully selecting the appropriate abrasive and pressure settings, sandblasting professionals can achieve optimal results while minimizing surface damage.
Benefits of Sand Blasting for Rust Removal
Rust compromises the integrity of metal structures, leading to costly repairs and replacements if not addressed promptly. Sand blasting for rust removal offers numerous benefits, making it a preferred method for restoring metal surfaces. One of the primary advantages is its efficiency; compared to manual rust removal techniques like wire brushing or chemical treatments, sandblasting completes the job faster and more effectively.
Another significant benefit is its ability to access hard-to-reach areas. Traditional rust removal methods struggle with intricate designs, crevices, and corners, but sandblasting can reach these spots effortlessly. This ensures a thorough cleaning, reducing the risk of residual rust that could cause future corrosion.
Moreover, sandblasting is environmentally friendly when using eco-friendly abrasives such as walnut shells, baking soda, or recycled glass. Unlike chemical rust removers, which may release harmful fumes, sandblasting minimizes exposure to toxic substances, making it a safer choice for workers and the environment.
Preventing Rust with Sandblasting
Beyond rust removal, sandblasting plays a crucial role in corrosion prevention. When a metal surface is stripped of rust and contaminants, it provides an ideal foundation for protective coatings. Paints, primers, and sealants adhere more effectively to a clean surface, enhancing their durability and longevity. By preventing rust with sandblasting, industries can reduce maintenance costs and extend the lifespan of their metal assets.
One of the key aspects of preventing rust is surface profiling. Sandblasting creates a slightly rough texture that improves the adhesion of protective coatings. This ensures that paints and primers bond securely, reducing the likelihood of chipping or peeling. Without proper surface preparation, coatings may fail prematurely, allowing moisture to penetrate and trigger corrosion.
Additionally, sandblasting removes old paint and corrosion inhibitors, ensuring that new coatings adhere to bare metal rather than deteriorated layers. This prevents underlying rust from spreading beneath the surface, maintaining the structural integrity of metal components. For industries that rely on metal structures, such as construction, automotive, and marine applications, preventing rust with sandblasting is a cost-effective strategy for long-term protection.
Industrial Applications of Sandblasting
The versatility of sandblasting makes it an essential process across various industries. In the automotive sector, it is used to restore vintage cars, remove rust from vehicle frames, and prepare surfaces for repainting. The aerospace industry also relies on sandblasting to maintain aircraft components, ensuring they meet safety and performance standards.
In construction, sandblasting is widely applied to clean steel beams, bridges, and pipelines. The removal of rust and old coatings enhances the durability of structures, preventing premature deterioration due to environmental exposure. Similarly, marine industries benefit from sandblasting in ship maintenance, where metal hulls require periodic rust removal to withstand harsh saltwater conditions.
Sandblasting is also common in manufacturing and industrial machinery maintenance. Factories and production facilities use this method to refurbish equipment, ensuring that machines operate efficiently without corrosion-related failures. Whether in large-scale industrial operations or small-scale restoration projects, sandblasting remains a critical technique for metal preservation.
Choosing the Right Sandblasting Method
Selecting the appropriate sandblasting method depends on the specific requirements of the project. Dry sandblasting is the most common approach, using compressed air to propel abrasive materials. However, wet sandblasting, which combines water with abrasives, is preferred for reducing dust and minimizing surface damage.
For delicate surfaces or precision work, soda blasting is an alternative that uses baking soda as an abrasive. This method is gentle on metal surfaces while effectively removing rust and paint. Similarly, vapor blasting utilizes a water-based slurry to clean and polish surfaces without causing excessive abrasion.
When considering sandblasting services, it is crucial to work with experienced professionals who understand the intricacies of different abrasives and techniques. Proper safety measures, such as protective gear and ventilation, should also be observed to prevent health risks associated with airborne particles.
Conclusion
Sand blasting for rust removal is a highly effective technique for restoring and maintaining metal surfaces. Its ability to remove rust efficiently, prepare surfaces for protective coatings, and contribute to corrosion prevention makes it a valuable tool across multiple industries. By preventing rust with sandblasting, businesses and individuals can extend the lifespan of metal structures, reduce maintenance costs, and ensure long-term durability. Whether for automotive restoration, industrial machinery maintenance, or construction projects, sandblasting remains a trusted solution for combating rust and corrosion.
Need Steel Fabricators in Hermiston, OR?
NW Metal Fabricators, Inc. is a family-owned business that has been servicing customers in Hermiston, Oregon since 1986. We have more than 100 years of experience in the food-processing industry and specialize in the custom production of storage bins, conveyors, catwalks, handrails, gates, storage tanks, water heater tanks, sanitary piping, steam piping, and trailer truck hitches. NW Metal Fabricators, Inc. is an accredited member of the local Chamber of Commerce. We are a dedicated business where quality always comes first. Our customers know that they can count on us to make sure that their products are hand-crafted to meet their specifications. Contact us today to learn more about what we can do for you!
Categorised in: Sandblasting
This post was written by admin