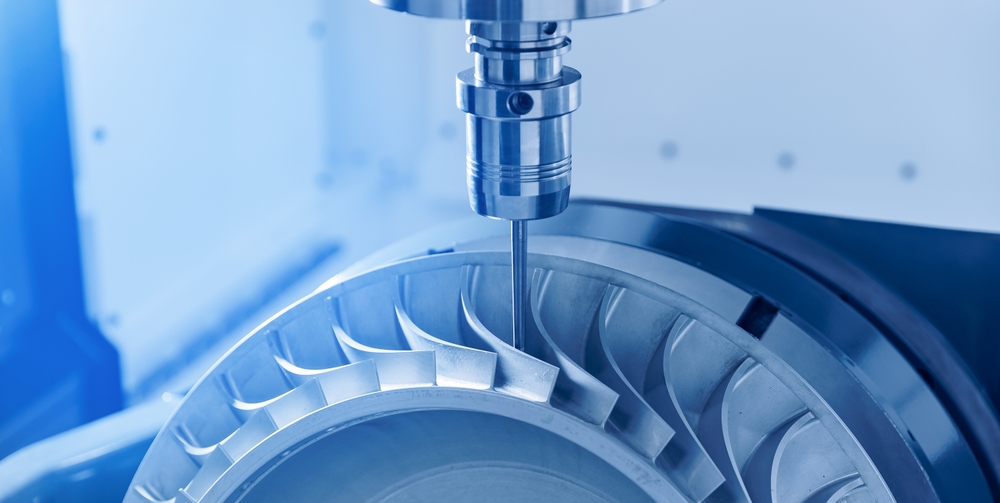
Advantages of 5-Axis Machining Over 3-Axis
September 10, 2024 1:36 pm Leave your thoughtsIn the world of precision manufacturing, machining technology continues to evolve, offering manufacturers new capabilities to enhance productivity and product quality. Among the various machining technologies, 5-axis machining has become a game-changer, providing significant advantages over the more traditional 3-axis machining. In this blog, we’ll explore the key benefits of 5-axis machining and how it compares to 3-axis machining, highlighting why more industries are making the switch.
3-Axis vs. 5-Axis Machining
Before diving into the advantages, it’s essential to understand the fundamental differences between 3-axis and 5-axis machining.
What is 3-Axis Machining?
3-axis machining is a traditional method that operates on three different axes: X, Y, and Z. The X and Y axes represent horizontal movement, while the Z axis represents vertical movement. This setup allows the cutting tool to move in three directions to create a part, typically in a linear manner.
What is 5-Axis Machining?
5-axis machining, on the other hand, introduces two additional rotational axes—usually referred to as the A and B axes. These additional axes enable the cutting tool to approach the workpiece from almost any direction. The added rotational movements provide greater flexibility and precision, allowing for more complex geometries and tighter tolerances.
Enhanced Precision and Accuracy
Superior Precision in Complex Parts
One of the primary advantages of 5-axis machining over 3-axis machining is its ability to produce highly accurate and complex parts. The additional rotational axes allow the tool to reach different angles and orientations without requiring the workpiece to be repositioned. This capability is particularly valuable for producing intricate components with complex geometries, such as those found in aerospace, medical devices, and high-precision engineering.
Reduction in Tool Wear and Tear
By enabling the tool to approach the workpiece from various angles, 5-axis machining can reduce the amount of tool deflection and wear. This reduction in tool wear leads to improved part consistency and longer tool life. In contrast, 3-axis machining often requires multiple setups and tool changes, which can contribute to increased wear and less precise results.
Increased Efficiency and Reduced Setup Time
Fewer Workpiece Repositions
In 3-axis machining, multiple setups are often required to complete a part, as the workpiece must be repositioned to access different faces and features. Each repositioning introduces the potential for error and requires additional time for alignment and setup. 5-axis machining minimizes or eliminates the need for multiple setups by allowing the cutting tool to access all sides of the workpiece in a single setup. This reduction in repositioning not only saves time but also enhances overall efficiency.
Faster Production Times
With fewer setups and reduced repositioning, 5-axis machining can significantly accelerate production times. The ability to complete complex parts in a single setup means that manufacturers can achieve higher throughput and meet tighter deadlines. This efficiency can lead to cost savings and improved competitiveness in the market.
Greater Flexibility in Machining Complex Geometries
Capability to Machining Multi-Sided Parts
5-axis machining excels in producing multi-sided parts that would be challenging or impossible to achieve with 3-axis machining. The additional axes provide the flexibility to machine complex contours, undercuts, and other intricate features with ease. This capability is especially beneficial for industries that require parts with complex shapes, such as automotive, aerospace, and mold making.
Improved Access to Hard-to-Reach Areas
Certain parts have features or pockets that are difficult to access with a standard 3-axis machine. 5-axis machining can reach these hard-to-reach areas more effectively, allowing for more comprehensive and detailed machining. This advantage is particularly useful for creating parts with deep cavities or intricate internal features.
Enhanced Surface Finish and Quality
Smoother Surface Finishes
The ability to machine parts from multiple angles in a single setup helps to achieve smoother surface finishes. 5-axis machining allows for more consistent tool paths and minimizes the need for rework or additional finishing processes. As a result, the surface quality of the final product is often superior compared to parts produced with 3-axis machining.
Reduced Need for Secondary Operations
By achieving higher precision and better surface finishes directly from the machining process, 5-axis machining often reduces the need for secondary operations, such as grinding or polishing. This reduction in secondary operations not only lowers production costs but also minimizes the risk of introducing errors or inconsistencies.
Cost-Effectiveness in the Long Run
Lower Production Costs
While the initial investment in 5-axis machining equipment may be higher compared to 3-axis machines, the long-term cost benefits are significant. The ability to complete complex parts in a single setup, combined with reduced tool wear and fewer secondary operations, can lead to substantial cost savings. Manufacturers often find that the increased efficiency and reduced production time offset the initial equipment costs.
Increased Profit Margins
With improved precision, faster production times, and reduced operational costs, manufacturers can achieve higher profit margins. The enhanced capabilities of 5-axis machining enable the production of high-quality, complex parts that command higher prices, further contributing to increased profitability.
Applications Across Industries
Aerospace and Defense
In the aerospace and defense industries, where precision and performance are critical, 5-axis machining is invaluable. It enables the production of intricate components with tight tolerances, such as turbine blades, aircraft structural parts, and missile components.
Medical Devices
The medical device industry benefits from 5-axis machining’s ability to produce highly accurate and complex parts. Components such as surgical instruments, implants, and prosthetics require precise machining to ensure proper fit and functionality.
Automotive
The automotive industry uses 5-axis machining to produce complex parts, including engine components, transmission housings, and custom parts for high-performance vehicles. The technology’s flexibility and precision contribute to improved performance and reliability in automotive applications.
Mold Making
Mold making is another area where 5-axis machining shines. The ability to machine complex mold cavities and features with high precision reduces the need for manual finishing and ensures that molds produce high-quality parts with minimal defects.
Conclusion
In summary, 5-axis machining offers a range of advantages over 3-axis machining, including enhanced precision, increased efficiency, greater flexibility, and improved surface finish. While the initial investment in 5-axis equipment may be higher, the long-term benefits in terms of cost-effectiveness and production capabilities make it a valuable technology for various industries. As manufacturing continues to advance, 5-axis machining stands out as a crucial tool for achieving superior results in complex and high-precision applications.
By understanding the difference between 3 and 5-axis machining and leveraging the advantages of 5-axis technology, manufacturers can stay ahead in the competitive landscape and deliver high-quality products with greater efficiency and precision.
Need Steel Fabricators in Hermiston, OR?
NW Metal Fabricators, Inc. is a family-owned business that has been servicing customers in Hermiston, Oregon since 1986. We have more than 100 years of experience in the food-processing industry and specialize in the custom production of storage bins, conveyors, catwalks, handrails, gates, storage tanks, water heater tanks, sanitary piping, steam piping, and trailer truck hitches. NW Metal Fabricators, Inc. is an accredited member of the local Chamber of Commerce. We are a dedicated business where quality always comes first. Our customers know that they can count on us to make sure that their products are hand-crafted to meet their specifications. Contact us today to learn more about what we can do for you!
Categorised in: Machining
This post was written by admin