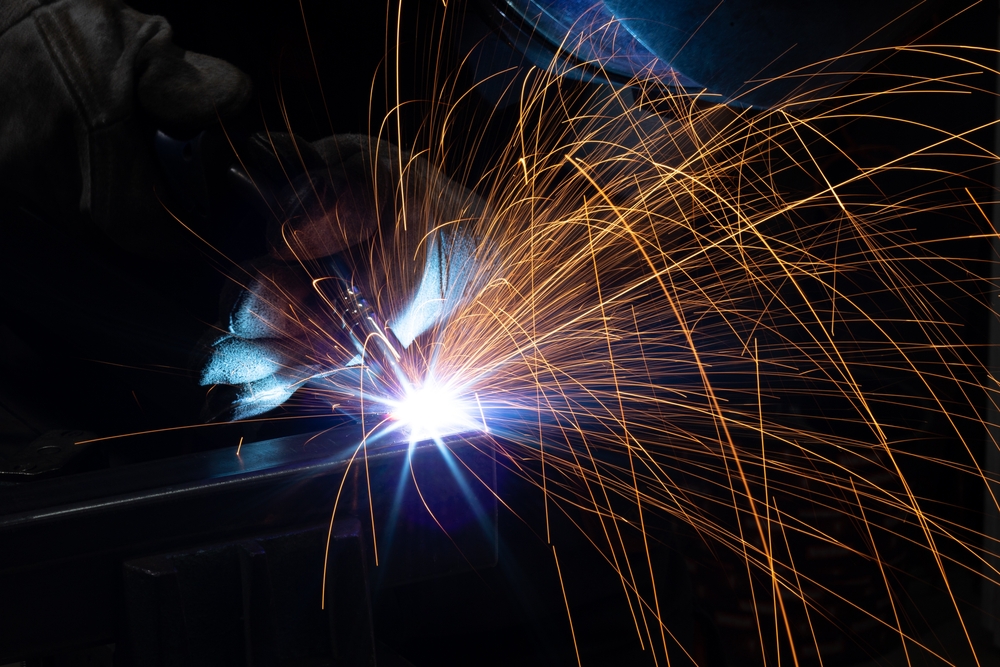
The Difference Between TIG and MIG Welding
August 13, 2024 6:38 pm Leave your thoughtsWelding is an essential process in various industries, from automotive repair to construction, and even art. Two of the most common welding techniques are TIG and MIG welding. Understanding the difference between TIG and MIG welding can help you choose the right method for your specific project needs. In this article, we will explore the key differences between TIG and MIG welding, their advantages and disadvantages, and applications to guide you in selecting the appropriate welding technique.
What is MIG Welding?
MIG welding, or Metal Inert Gas welding, is a type of welding that uses a continuous wire feed as the electrode. This method involves feeding a wire through a welding gun, which melts the wire and joins it with the base metal. The process is shielded by an inert gas, typically argon or a mixture of argon and carbon dioxide, to protect the weld from contamination and oxidation.
Advantages of MIG Welding
- Ease of Use: MIG welding is often recommended for beginners because it is relatively easy to learn. The continuous wire feed simplifies the process, making it easier to produce consistent welds.
- Speed: MIG welding is generally faster than other welding methods. The continuous feed allows for quicker welds, which can be advantageous in high-production environments.
- Versatility: MIG welding can be used on a wide range of materials, including steel, aluminum, and stainless steel. It is also effective on different thicknesses of material.
- Minimal Clean-Up: The inert gas shielding helps reduce the amount of spatter and cleanup required after welding.
Disadvantages of MIG Welding
- Equipment Cost: MIG welding equipment can be expensive, particularly for high-quality machines. Additionally, the cost of shielding gases and consumables can add up over time.
- Outdoor Limitations: MIG welding is less effective in windy conditions, as the shielding gas can be blown away, leading to contamination of the weld.
- Thickness Limitations: While MIG welding is versatile, it may not be suitable for very thin materials or very heavy-duty applications.
What is TIG Welding?
TIG welding, or Tungsten Inert Gas welding, involves a non-consumable tungsten electrode to produce the weld. The process uses an inert gas, typically argon, to shield the weld area from atmospheric contamination. TIG welding allows for more precise control over the weld, making it ideal for detailed and high-quality work.
Advantages of TIG Welding
- Precision: TIG welding provides greater control and precision, allowing for high-quality welds on thin and delicate materials. This makes it ideal for applications where appearance and accuracy are crucial.
- Clean Welds: TIG welding produces clean and smooth welds with minimal spatter. This is especially important in applications where aesthetics and cleanliness are a priority.
- Versatility: TIG welding is highly versatile and can be used on a variety of materials, including aluminum, magnesium, and stainless steel. It is also effective for welding thin sections of metal.
- No Spatter: Because TIG welding does not use a filler rod in the same way as MIG welding, there is typically no spatter, reducing post-weld cleanup.
Disadvantages of TIG Welding
- Learning Curve: TIG welding has a steeper learning curve compared to MIG welding. It requires more skill and practice to master the technique and achieve consistent results.
- Slower Process: TIG welding is generally slower than MIG welding, which can be a disadvantage in high-production environments where speed is crucial.
- Higher Cost: TIG welding equipment tends to be more expensive, and the process can also be more labor-intensive due to the need for precision and control.
Key Differences Between MIG and TIG Welding
Electrode Type
- MIG Welding: Uses a continuous wire feed as the electrode.
- TIG Welding: Uses a non-consumable tungsten electrode.
Shielding Gas
- MIG Welding: Typically uses a mixture of argon and carbon dioxide or pure argon as shielding gas.
- TIG Welding: Uses pure argon or helium as shielding gas.
Filler Material
- MIG Welding: Filler material is supplied continuously through the welding gun.
- TIG Welding: Filler material is fed manually by the welder and is not continuously supplied.
Application
- MIG Welding: Best suited for thicker materials and high-speed applications. Ideal for general fabrication and automotive repairs.
- TIG Welding: Best for thin materials and applications requiring high precision and clean welds. Commonly used in aerospace, automotive, and artistic welding projects.
Ease of Use
- MIG Welding: Easier to learn and use, making it suitable for beginners.
- TIG Welding: Requires more skill and practice, suited for more experienced welders.
Choosing the Right Welding Method
When deciding between MIG and TIG welding, consider the following factors:
- Material Type and Thickness: MIG welding is generally better for thicker materials and a wider range of metals. TIG welding excels with thin materials and provides cleaner welds.
- Welding Speed: If speed is a priority, MIG welding is the faster option. TIG welding is slower but offers greater precision.
- Weld Quality: For projects requiring high-quality, clean welds, TIG welding is the better choice. MIG welding is suitable for general applications where appearance is less critical.
- Skill Level: Beginners might find MIG welding easier to learn and use, while TIG welding is better suited for those with more experience or those who need to produce high-precision welds.
Conclusion
Understanding the difference between TIG and MIG welding is crucial for selecting the right technique for your project. MIG welding offers ease of use, speed, and versatility, making it suitable for a wide range of applications and skill levels. TIG welding, on the other hand, provides superior precision and clean welds, ideal for detailed and high-quality work. By considering factors such as material type, welding speed, and skill level, you can choose the welding method that best meets your needs.
Need Steel Fabricators in Hermiston, OR?
NW Metal Fabricators, Inc. is a family-owned business that has been servicing customers in Hermiston, Oregon since 1986. We have more than 100 years of experience in the food-processing industry and specialize in the custom production of storage bins, conveyors, catwalks, handrails, gates, storage tanks, water heater tanks, sanitary piping, steam piping, and trailer truck hitches. NW Metal Fabricators, Inc. is an accredited member of the local Chamber of Commerce. We are a dedicated business where quality always comes first. Our customers know that they can count on us to make sure that their products are hand-crafted to meet their specifications. Contact us today to learn more about what we can do for you!
Categorised in: Welding
This post was written by admin